Gowanus Facilities Upgrade
THOUGHTFUL DESIGN RESTORES GRANDEUR OF HISTORIC STRUCTURES WHILE ADDING SLEEK NEW SERVICE FACILITY AND PUMP STATION
Built in the mid-1800s, the Gowanus Canal was a hub of Brooklyn’s maritime and commercial shipping activity. It teemed with factories, warehouses, tanneries, coal stores, and manufactured gas refineries. After years of use, unregulated sewage, and industrial discharges, the canal became one of the most heavily contaminated water bodies in the U.S.
As a step toward improving Gowanus Canal water quality, the New York City Department of Environmental Protection (DEP) launched a $183 million facilities upgrade to increase the capacity, function, and reliability of the canal flushing tunnel system and wastewater pumping station. The project included the renovation of two historic buildings, the construction of a new service facility and sewage pumping station, and the restoration of a stately perimeter wall around the canal facilities.
What We Did
The design team set out to preserve the historic character of the original Dutch Colonial buildings, while infusing the site with a modern style symbolic of its renewal. The 3,550-square-foot Flushing Tunnel Building and 630-square-foot Gate House suffered from aging doors, windows, and roofs, damaged masonry, as well as abandoned piping, conduits, and equipment hangers. Their rehabilitation included exterior maintenance improvements, such as repointing, repairing the roofs, and resetting the limestone copings and keystones that had shifted over time. In the Flushing Tunnel Building, all six of the dormer windows and two of the rear facing arched windows were replaced with architectural louvers to provide increased ventilation required by the mechanical upgrades.
The sleek new 5,400-square-foot Service Building and Pumping Station features stainless steel panels, which alternate with stainless steel louvers, stainless steel coiling doors, and stainless steel swing doors. This façade material offered a solution to a practical challenge: the stainless steel panels allowed the building to be taller to accommodate the mechanical equipment and were also lightweight enough to be supported by the existing foundation. Designers also creatively linked the Service Building to the adjacent Flushing Tunnel Building by using one of the historic structure’s arches on the façade as the connection entrance. The strategic placement minimized the impact to the historic buildings and created an efficient passage. At the community’s request, the 200-foot-long Butler Street Wall, which encloses the property, was carefully redesigned and reconstructed to preserve its historic charm.
Key Features
- Rehabilitation preserved the historic buildings’ original design while improving function and strength.
- New stainless steel Service Building serves as a visual symbol of modern improvements.
- Restored Butler Street Wall maintains its original proportions, arches, and recognizable characteristics.
- Curving parapets conceal mechanical rooftop units on the new Service Building.
Outcomes
- Renovations to the Tunnel Building and Gate House restore their historic charm.
- New stainless steel service facility adds a contemporary feel to the site.
- Perimeter wall reconstructed in keeping with original design.
- Sustainable features protect an environmentally damaged area.
- Entire project provides a catalyst for local economic resurgence.
- High reflectance, single-ply roof material reduces heat gain.
- 600-square-foot green roof reduces stormwater runoff.
- 30 percent of limestone and 80 percent of original granite reused.
- Rehabilitated pumping station expected to lower possible sewage overflow into waterway by 50 percent.
CLIENT
New York City Department of Environmental Protection
LOCATION
Brooklyn, N.Y.
ROLE
Architecture, Structural, Geotechnical
Related Projects
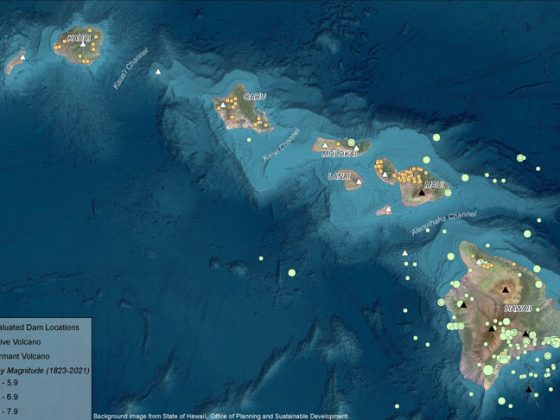